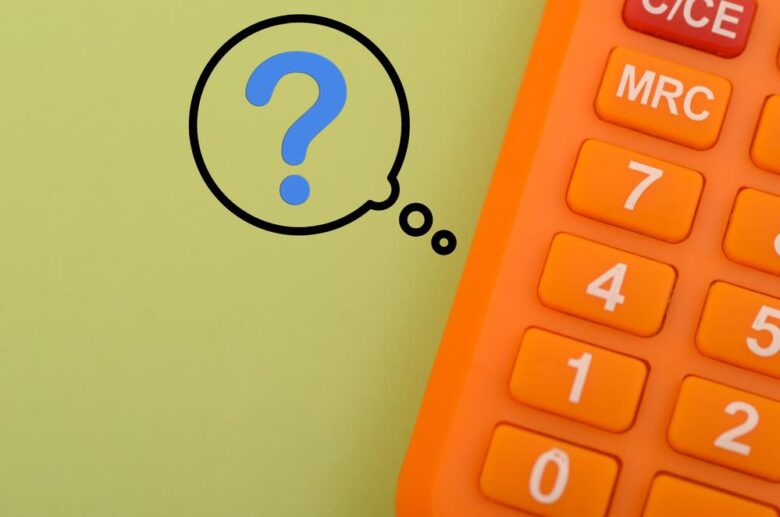
「棚卸しを実施したら予想以上に差異が出た。どうして差異が出たのか。差異が大きいとどうなるのか。」
「棚卸しの差異が大きかったので減らしたい。」
実際の在庫の数量と帳簿上の在庫の数量は本来一致しているはずなのに、棚卸しを行うと差異が出てきて悩んでいる人も多いと思います。
棚卸しの差異は、棚卸し作業時のミスだけでなく、日々の入荷・保管・出荷、それに紐づくデータ処理の中でミスが起きることにより発生します。
その大半は、数え間違いや入力ミス・漏れなどのヒューマンエラーによって起きるものです。
ヒューマンエラーをなくすためには、システム導入による自動化と、業務の見直しが効果的です。
本記事で紹介する対策をしっかりと講じて、差異をなくしていくようにしましょう。
差異が大きいのに対策を行わないと、経営にさまざまな悪影響を及ぼします。
差異が発生する状況を放置していれば、いずれ在庫不足が生じ、「発注を受けて出荷しようとしたら在庫がない」「部品の在庫が切れて生産がとまった」というトラブルも招きかねません。
このようなトラブルを防ぐためにも、差異の重大性を理解し、差異のない在庫管理を目指していきましょう。
【本記事で分かること】
・棚卸しで差異が起きる原因 ・差異が大きいことによる悪影響 ・差異率の許容範囲と目指すレベル ・棚卸しの差異をなくすための対策 |
本記事を読めば、差異について理解したうえで、差異の原因と対策が分かり、実践できるようになります。
ぜひ最後まで読んでいってくださいね。
目次
1.棚卸しで差異が起きる原因
棚卸しで差異が起きる原因はいくつかあります。
差異が起きやすい場面と、差異の原因について下表にまとめました。
【棚卸し差異が起きる原因】
原因 | 内容 | |
棚卸し | カウントミス | ・数量を数え間違える ・数え漏れが起きる ・同じものを重複して数えてしまう |
入荷時 | 仕入先の納品ミス | ・仕入先から納品された商品の数量が、発注していた数量と異なる |
保管時 | 紛失・盗難 | ・適切に管理できておらず、紛失や盗難が起こってしまう |
出荷時 | 誤出荷 | ・ピッキングや梱包時に数量を間違えて出荷してしまう |
データ処理 | 入力ミス・漏れ | ・数量を誤って入力してしまう ・入力が漏れてしまう |
上記のとおり在庫の差異は、棚卸し時のカウントミスだけでなく、入荷から出荷までの日々の業務の中で発生する差異も多く含まれます。
つまり、棚卸しの時に出る差異は、日々の在庫管理の精度の結果と言えます。
在庫の差異は、現品か在庫表どちらかの数量に間違いが生じることで発生しますが、その多くは「数え間違い」や「作業漏れ」などのヒューマンエラーが原因です。
人が作業する以上ヒューマンエラーが発生するのは仕方ありませんが、それが多すぎると経営に悪影響が出るため、差異を減らすための対策を実施していくことが求められます。
2.差異が大きいとどうなるのか?差異による悪影響
在庫の差異が大きいことは、経営にどのような悪影響を及ぼすのでしょうか。
差異の問題点について、3つ紹介していきます。
【在庫差異による悪影響】
1.調査・会計処理・報告書作成など、業務が増える 2.在庫切れが発生し、販売機会を逃してしまう(実際の在庫数の方が少ない場合) 3.過剰在庫になり、無駄な費用がかかる(実際の在庫数の方が多い場合) |
2-1.調査・会計処理・報告書作成など、業務が増える
差異が大きいと、調査や後処理の業務が増え、棚卸しにかかる時間が長引いてしまいます。
差異が大きいことで発生する業務を下表にまとめました。
【差異が大きいと増える業務】
増える業務 | 具体例 |
調査 | ・重要な商品がデータより少ない場合、倉庫中を探し回る |
会計処理 | ・現品が在庫データより少ない場合は「棚卸減耗費」として、多い場合は「繰越商品」として仕訳する |
伝票・在庫データの調整 | ・新たに伝票を発行する |
報告書作成 | ・差異の原因を特定して再発防止策を記載する |
上記のとおり、差異が大きいほど業務は増え、担当者の負担が大きくなってしまうでしょう。
2-2.在庫切れが発生し、販売機会を逃してしまう(実際の在庫数の方が少ない場合)
現品が在庫データより少ない場合、在庫切れが発生し、販売機会を逃してしまうおそれがあります。
データ上はまだ在庫が十分あるので発注を受けると、いざ出荷しようと思ったときに「在庫がない!」という状況に陥ることが考えられます。
発注はキャンセルとなり、販売機会を逃してしまううえ、顧客が離れていく要因にもなるでしょう。
製造業の場合は、部品や材料が在庫切れになると、最悪生産がストップしてしまうおそれがあります。
人件費などが無駄になり、後工程にも遅れが生じて、大きな損失を招いてしまうでしょう。
2-3.過剰在庫になり、無駄な費用がかかる(実際の在庫数の方が多い場合)
現品が在庫データより多い場合は、過剰在庫になり、無駄な費用がかかるおそれがあります。
データ上の在庫が少なくなったと思って発注すると、実際には棚にはまだ在庫があり、過剰在庫となってしまいます。
もし販売・出荷しきれなかった場合は、廃棄処分となり、購入費と処理費用が無駄にかかってしまうでしょう。大きいものなら保管場所も圧迫してしまいます。
3.棚卸しの差異率の許容範囲は5%・目標値2%
棚卸しの差異はどれくらいあると「多い」のでしょうか。そして、どのくらいまで減らすことを目標とすればいいのでしょうか。
自社の差異の状況を把握するために、まずは棚卸しの差異率を計算する必要があります。
差異率とは、実際の在庫の数量とデータ上の在庫数の差を割合で表したもので、在庫管理の精度をはかる指標となります。
差異率について、次の順に見ていきましょう。
【棚卸しの差異率】
・差異率の許容範囲と目標値 ・差異率の計算方法 ・差異率を出すときの注意点|商品ごとに計算が必要 |
3-1.差異率の許容範囲と目標値
差異率は、一般的に5%以下であれば許容範囲とし、2%を目標値に掲げている企業が多いです。
しかし、実際には差異が1%出ても許容できない商品もあるので、価格や特性をふまえたうえで、各社が適切な数値を設定しましょう。
3-2.差異率の計算方法
差異率の出し方は下記のとおりです。
【差異率の計算方法】
差異率 = 1 ー 実際の在庫数 ÷ データ上の在庫数 × 100 |
たとえば、実際の在庫数が98個で、データ上の在庫数が100個だった場合、差異率は次のように計算します。
差異率 = 1 ー 98(実際の在庫数) ÷ 100(データ上の在庫数) × 100 =2%
この場合、差異率は2%であることが分かります。
3-3.差異率を出すときの注意点|商品ごとに計算が必要
差異率を出すときの注意点として、計算は商品ごとに出さなければいけません。
なぜなら、まとめて計算すると、マイナスの差異とプラスの差異が混ざってしまうからです。
【参考】
マイナスの差異→棚卸差損:データ上の在庫より実際の在庫の方が少ない プラスの差異→棚卸差益:データ上の在庫より実際の在庫の方が多い |
全在庫で計算した場合、下記の例のとおり差異率を正しく計算できません。
【例】
商品A:実際の在庫数が98個・データ上の在庫数が100個→差異率= -2% 商品Aと商品Bを合わせると…差異率0%になってしまう! |
差異率を正確に把握するためには、マイナスとプラスを混合しないように注意しましょう。
4.棚卸し差異を減らす2通りの対策・「業務見直し」「システム導入」どちらがいい?
ではあらためて、棚卸しの差異をなくすためにはどうすべきかを見ていきましょう。
差異を少なくする方法は、「業務見直し」と「システム導入」の2通りあります。
【棚卸の差異をなくす方法】
まずは 《業務見直し》 | ・業務体制の整備はヒューマンエラーを減らす基本的な対策 |
業務体制を整えても差異が大きいなら 《システム導入》 | ・手作業→自動化により、大幅な差異削減を期待できる |
まず、差異を減らすためには、業務見直しから取り組みましょう。
業務体制が整備されていないと、従業員によって業務のやり方やレベルにバラつきが出てしまい、トラブルの発生につながります。
また、従業員が余計な負担を感じてしまうと、集中力を欠くことになり、ミスが起きやすくなるでしょう。
ヒューマンエラーをなくすためには、業務を正確に進めるための業務フロー・ルール・環境を整備することが重要です。
差異率が大きい企業は、業務体制を万全に整えるだけでも、差異減少の効果を期待できます。
しかし、業務体制は整っているのに差異が大きいケースは、システム導入をおすすめします。
差異の原因は主にヒューマンエラーであることから、手作業を続ける限り、差異削減の対策には限度があります。
システムを活用すれば業務を自動化できるため、大幅な差異削減を期待できるでしょう。
【対策の進め方まとめ】
まずは5章「業務見直し」の方法を見て、自社が適切に実行できているか確認 |
5.差異をなくすための対策【業務見直し】
まずは【業務見直し】による対策を紹介していきます。
共通と場面別の対策方法を下表にまとめました。
【共通の対策】
・マニュアルを作成し、従業員に周知する ・ダブルチェック体制で行う(2通りのチェック方法で実施) ・整理整頓を行う |
【場面別の対策】
原因 | 対策 | |
棚卸し | カウントミス | ・事前準備をしっかり行う |
入荷時 | 仕入先の納品ミス | ・仕入先に対策をしてもらう |
保管時 | 紛失・盗難 | ・3定管理を徹底する |
出荷時 | 誤出荷 | ・共通の対策を徹底する |
データ処理 | 入力ミス・漏れ | ・数字やアルファベットの書き方を統一する |
棚卸しの精度は日々の積み重ねの結果ですので、上記のような業務の基本を確実におさえていくことが大切です。
共通の対策と、原因ごとの対策をひとつずつ見ていきましょう。
POINT! 場面別、どれから取り組むべき?ーーまずは棚卸しのカウントミスから 理由(1)棚卸しのカウントミスは、実際の在庫とは違う数量を、帳簿に記載することになるからです。 理由(2)もうひとつの理由としては、棚卸しのカウントミスは、対策を実行しやすいからです。 ほかの原因と違い日々の業務で起こる差異ではなく、棚卸しの場面だけに限られているので、すぐに改善に取り組むことができます。 以上のことから、差異をなくしたいのなら、まずは棚卸しを見直すようにしましょう。 |
5-1.共通の対策
最初に差異をなくす共通の対策を見ていきましょう。
【差異を防ぐための対策】
・マニュアルを作成し、従業員に周知する ・ダブルチェック体制で行う(2通りのチェック方法で実施) ・整理整頓を行う |
上記の内容はすべて在庫を持つ企業・店舗では基本的なことですが、多くの在庫を適切に管理するためには欠かせない内容です。
不十分なところはないか今一度確認して、実行するようにしましょう。
5-1-1.マニュアルを作成し、従業員に周知する
業務のミスをなくすためには、作業手順やルールを明確化したマニュアルを作成することが効果的です。
マニュアルがあることによって業務を標準化でき、経験が浅い従業員でも、ミスなくスムーズに業務を行えます。
ミス削減に効果的なマニュアル作成のポイントは下記のとおりです。
【マニュアル作成のポイント】
・返品・破損・サンプル出荷など、イレギュラーな業務の対処法も定めておく ・理由の説明(なぜこの作業が必要なのか、なぜこの手順で行うのか)も付けておくと納得しやすい ・過去にあったミスの事例なども共有し、注意喚起を促す ・現場からも意見やアイデアを出してもらう ・定期的に更新する |
マニュアルがあっても、独自のやり方に変えていってしまう人もいます。
マニュアルはこれまでの経験を集結させ、ミスを生まないために作成されたものであることをしっかりと伝え、マニュアルどおりに業務を進めるよう教育を徹底しましょう。
5-1-2.ダブルチェック体制で行う(2通りのチェック方法で実施)
ダブルチェックを行うことは、ミスを防ぐうえで有効な方法です。
もしミスがあっても、後からチェックする人が見つけて防ぐことができるからです。
しかし、ダブルチェックは後からチェックする人が、「たぶん合っているだろう」という思い込みを持ちやすく、チェックがあまくなってしまいがちですよね。
そこでおすすめなのが、1人目と2人目の作業者でチェック方法を変えるという方法です。
たとえば、1人目は商品番号でチェックし、2人目は商品名でチェックを行うといういうような方法です。
これなら2人目の作業者も作業の意義を見出しやすく、集中して取り組みやすいでしょう。
5-1-3.整理整頓を行う
整理整頓を行うことも、ミスを減らすうえで基本かつ重要なことです。
倉庫や作業場が乱雑な状態だと、何がどこにあるか分かりづらく、業務の精度を下げてしまいます。ほかの商品が混在しても見つけづらく、紛失したものを探し出すことも一苦労でしょう。
また、余計な物が多いと十分なスペースを確保しづらいため、作業ストレスがかかり、間違いもおこりやすくなります。
不要な物は処分して、「何がどこにあるか」がすぐに分かる環境を整えましょう。
5-2.棚卸しのカウントミスの対策
棚卸しのカウントミスとは、数量を正しく数えられないことにより、実際の数量とは違う数字を報告してしまうことです。
【カウントミスの具体例】
・数量を数え間違える ・数え漏れが起きる ・同じものを重複して数えてしまう |
カウントミスを防ぐための対策としては、下記2点が有効です。
【カウントミスを防ぐための対策】
・事前準備をしっかり行う ・細部までルールを設定し、作業者と共有する |
5-2-1.事前準備をしっかり行う
まずは事前準備をしっかり行うことが、カウントミスの削減への第一歩です。
準備が十分でないと、当日さまざまな対応に追われ、「数量を数える」作業に専念できません。
結果、カウントミスが起こりやすくなります。
たとえば、在庫が乱雑に配置されていると、どこから数え始めるべきか迷ったり、同じ商品を重複して数えたりするおそれがあるでしょう。
また、作業の遅延やトラブルも起こりやすく、作業者に混乱と焦りが生じ、さらに数え間違いを引き起こしてしまいます。
このようなことがないよう、当日はカウント作業だけに集中できる環境を整えていきましょう。
事前にしっかり準備しておきたいことは下記のとおりです。
【事前に準備しておきたいこと】
・対象在庫の洗い出し ・適切な時間配分の設定 ・作業員の人選と配置決め ・作業環境の整備 ・作業に必要な道具などの準備 |
5-2-2.細部までルールを設定し、作業者と共有する
細部までルールを設定するのも、カウントミス削減に効果的です。
数え方が統一されておらず、作業員が自分のやり方で数えると、混乱や重複、漏れの原因になります。
たとえば、物の数え方は箱単位なのか個単位なのかを決めておかないと、作業者によってバラつきが出てしまいますよね。
細部までルールを徹底することで、誰が数えても同じ数量を出せるようになるでしょう。設定しておきたいルールの一例を下表にまとたので、参考にしてください。
【棚卸しで決めておきたいルール(例)】
・数える単位(例:小袋単位か、中身の個数単位か) ・数える順番(例:左上・手前から) |
5-3.入荷時の仕入先による納品ミスの対策
仕入先に入荷時の検品ミスとは、仕入先から納品された商品の数量が、発注していた数量と異なっており、それに気づかず入荷してしまう状況です。
納品ミスを防ぐための対策としては、下記2点が挙げられます。
【納品ミスを防ぐための対策】
・仕入先に対策をしてもらう ・検品を行う・やり方を見直す |
5-3-1.仕入先に対策をしてもらう
納品ミス自体は仕入先の課題であるため、まずは仕入先に対策をしてもらう必要があります。
頻繁にミスが起こっているなら、改善に向けての取り組むよう要求するようにしましょう。
相手先から、「なぜ納品ミスが多いのか、ミス削減のためにどのような対策を講じるか」を報告してもらうと安心です。
5-3-2.検品を行う・やり方を見直す
仕入先のミスは、検品を行うことで防げます。
とはいえ、「検品ならすでに行っている」「検品してるのに差異を見逃してしまう」というケースも多いと思います。
検品を効率良く、かつ高い精度で行うためには、下記ポイントを意識してやり方を見直してみましょう。
【入荷検品】
・受取→検品→入庫の導線を動きやすくする ・検品場所を広く確保する ・入荷スケジュールを共有する |
いずれも基本的な内容ですが、検品作業に集中できる環境づくりが大切です。
5-4.保管時の紛失・盗難の対策
保管時の紛失・盗難とは、入荷から出荷(または棚卸し)までの間に、現品がなくなっている状況です。
紛失・盗難を防ぐための対策としては、下記2点が挙げられます。
【紛失・盗難を防ぐための対策】
・3定管理を徹底する ・視覚化を進める |
5-4-1.3定管理を徹底する
商品の保管方法は、「3定管理」を取り入れるのがおすすめです。
3定とは、「定位・定品・定量」の略であり、つまり「決められた場所に、決められた物を、決められた量だけ置く」という管理方法です。
3定管理を徹底することで、「どこに何がどれだけあるか」が一目で分かるので、商品の紛失を防ぎやすくなるでしょう。
5-4-2.視覚化を進める
視覚化を進めることも、紛失・盗難の防止に効果があります。
たとえば、商品の写真を棚に貼っておくと、違う商品を置こうとしたとき、写真が目に入るので、間違っていることに気づきやすくなります。ほかにも、種類ごとに色分けする方法なども有効です。
保管のルールを設定するだけでは不十分なので、直感的に正しい動作を行えるような工夫を取り入れていくようにしましょう。
5-5.出荷時の誤出荷の対策
出荷するときに、商品や数量を誤ってピッキングしたり、梱包時に入れ忘れてしまったりすることも差異の原因のひとつです。
誤出荷を防ぐためには、5-1.共通の対策を徹底することが何よりも重要です。
【差異を防ぐための対策】
・マニュアルを作成し、従業員に周知する ・ダブルチェック体制で行う ・整理整頓を行う |
出荷は特に、納入先に合わせて個別の対応が求められることが多く、熟練の人でも間違ってしまうことがあります。
誤出荷は後処理も大変であるうえ、顧客からの信頼を失うおそれがあります。基本の対策にしっかりと取り組むようにしましょう。
5-6.データ処理時の入力ミス・漏れ
現品に動きがあったのに、データの方に反映されていない、または情報が間違って入力されると、在庫に差異が発生してしまいます。
入力ミス・漏れを防ぐための対策としては、下記2点が挙げられます。
【入力ミス・漏れを防ぐための対策】
・数字やアルファベットの書き方を統一する ・入力漏れに気づける仕組づくりをする |
5-6-1.数字やアルファベットの書き方を統一する
数字やアルファベットの書き方を統一することで、転記ミスを防げます。
現場では手書きの作業も多いですが、数字やアルファベットには似たような文字が多く、見間違いの原因となります。
しっかりと区別できるよう、書き方に統一のルールを設定しましょう。
書き分け方の例を下表にまとめたので、参考にしてください。
【数字・アルファベットの書き分け方】
似ている数字 | 書き分け方の例 |
数字0とアルファベットO | ・数字0の真ん中に斜め線を引く |
数字2とアルファベットZ | ・アルファベットZの真ん中に斜め線を引く |
数字1と数字7 | ・数字7の真ん中に斜め線を引く |
アルファベット小文字l(エル) | ・アルファベット小文字lは筆記体で書く |
5-6-2.入力漏れに気づける仕組づくりをする
入力漏れに関しては、漏れがあることに気づける仕組づくりを徹底することが大切です。
まず、現品に動きがあったら、その情報が必ずデータ処理担当者に回ってくるようにしましょう。
そして、データ処理に期限を設け、処理がされないとアラートが出る仕組を構築しておきます。
たとえば、現場作業者は出荷を終えると伝票などを入力担当者に回し、その一方で伝票番号を記載したその日の出荷済リストを入力担当者の上長に回します。
入力担当者の上長はリストを見て、一定期間処理されていない伝票があると、漏れに気づけるという仕組です。
このように、現場と事務が連携して情報の流れを可視化し、確認の仕組みを整えることが重要です。
6.差異をなくすための対策【システム導入】
続いて、【システム導入】による対策について、下記順に紹介していきます。
【システム導入】
・差異をなくすのに効果的なシステムの種類 ・システム導入による差異削減の効果 ・システムの費用 |
6-1.差異をなくすのに効果的なシステムの種類
在庫差異をなくすためには、「在庫管理または倉庫管理システム」に「商品情報を読み取る機器」を組み合わせて活用することが効果的です。
【システム】
在庫管理システム | ・適切な在庫量の維持が目的 |
倉庫管理システム(WMS) | ・倉庫内の業務効率化が目的 |
【主な商品情報を読み取る機器】
ハンディターミナル | バーコードやQRコードなどを読み取ることで商品情報を取得する(数量はひとつずつ読み取るか、テンキー入力をする) |
スマートフォン | |
RFIDタグ対応 ハンディターミナル | 専用タグがついている一定距離内の商品の、情報と数量を一括で取得する(あらかじめ商品にRFIDタグを付ける必要がある) |
重量センサー | 計量器で商品の重さを箱ごと(カゴや袋など)はかることで、数量を自動で割り出す(商品情報は事前登録) |
システムだけでも差異を減らす効果はありますが、「商品情報を読み取る機器」と一緒に使用することで、より効果が高まるでしょう。
システムと商品情報を読み取る機器がセットで提供されているものも多く販売されています。
6-2.システム導入による差異削減の効果
システム導入により、2つの差異削減を期待できます。
【システム導入による差異削減の効果】
・転記・入力ミス・漏れ削減 ・カウントミス削減(RFID・重量センサー) |
6-2-1.転記・入力ミス・漏れ削減
システムを利用すれば、「商品情報を読み取る機器」から検品・カウントデータをシステムに送信できるので、転記・入力ミス・漏れを削減できます。
「在庫管理システムとハンディターミナル」を使用した場合の、入荷作業の流れを見てみましょう。
【例】
(1)システムで発注伝票から入荷指示書を自動作成・印刷 (2)入荷指示書に印刷されたバーコードをハンディターミナルで読み取る (3)ハンディターミナルで入荷商品のバーコードを読み取り、数量を数えてテンキー入力する (4)ハンディターミナルからデータを送信し、システムに反映される |
上記(3)(4)のとおり、ハンディターミナルの検品情報はそのままシステムに送信できるので、手作業で在庫データを更新する必要がなく、ミスの発生を防ぐことができます。
出荷・棚卸しの作業でも、同様の効果を期待できるでしょう。
6-2-2.カウントミス削減(RFID・重量センサー)
RFIDタグや重量センサーを活用する場合は、数量を自動で読み取れるので、カウントミスを削減できます。
それぞれの入荷作業の流れを見てみましょう。
【例】
《RFIDタグ(すでに商品にRFIDタグがついている場合)》 《重量センサー》 |
上記のとおり、RFIDタグや重量センサーを活用すると、「手作業で数える」という作業がないため、カウントミスを防ぐことができます。
出荷・棚卸し作業も同様で、特に棚卸しは作業効率も大幅な向上が期待できるでしょう。
6-3.システムの導入費用
システム導入で気になるのはコスト面ですよね。
下表に種類ごとの費用相場をまとめました。
【システム導入の費用】
システム | 購入の場合:約50万円~300万円 |
ハンディターミナル | 約5万円~20万円/台 (RFID対応は高くなる) |
スマートフォン | 従業員用のスマートフォンを利用できれば無料 |
RFIDタグ | 10円~50円/枚(電池内臓タイプは500円以上) |
重量センサー | 計量器:約1万円~5万円(高機能なものや特大サイズを除く) |
金額はシステムの種類や内容によって大きく異なります。
最新技術を搭載したシステムは高額ですが、小規模事業向けのシステムやアプリなどは低コストで利用できるでしょう。
利用料の負担は大きいですが、システムを活用による作業効率化で、人件費を抑えることができ、差異発生の対応のためのコストも削減できます。
現代はデジタル技術が広く普及し、在庫管理はシステム活用が主流となってきました。
業界でおくれをとらないためにも、システム導入は前向きに検討していくようにしましょう。
在庫管理の精度を高めたいなら! |
日々の在庫管理と棚卸しの正確性を高めたいなら、BtoB受発注システム「WONDERCART(ワンダーカート)」の導入がおすすめです。 WONDERCARTは、注文管理や在庫管理などの対応をオンラインで一元化します。 正確な在庫状況を、リアルタイムで確認できるので、在庫の差異をすぐに発見することができるでしょう。 「在庫管理の精度をもっと高めたい」とお考えの方は、ぜひご検討ください。 オンラインカタログと受発注管理機能を備えた「WONDERCART」について、さらに詳しく知りたい方は、こちらからご覧ください。 |
7.まとめ
あらためて本文の要点を振り返りましょう。
棚卸しの差異は、棚卸し作業時のミスだけでなく、日々の入荷・保管・出荷、それに紐づくデータ処理の中でミスが起きることにより発生します。
差異の度合いは、下記計算方法で算出してください。差異率の許容範囲は5%が目安です。
【差異率の計算方法】
差異率 = 1 ー 実際の在庫数 ÷ データ上の在庫数 × 100 |
差異が大きいと下記のような悪影響を及ぼすので、しっかり対策を行って差異を減らしていくようにしましょう。
【在庫差異による悪影響】
1.調査・会計処理・報告書作成など、業務が増える 2.在庫切れが発生し、販売機会を逃してしまう(実際の在庫数の方が少ない場合) 3.過剰在庫になり、無駄な費用がかかる(実際の在庫数の方が多い場合) |
差異を減らす対策としては、「業務見直し」と「システム導入」が有効です。
「業務見直し」では、下記項目で実施できていない部分があれば、漏れなく対処するようにしましょう。
【共通の対策】
・マニュアルを作成し、従業員に周知する ・ダブルチェック体制で行う(2通りのチェック方法で実施) ・整理整頓を行う |
【場面別の対策】
原因 | 対策 | |
棚卸し | カウントミス | ・事前準備をしっかり行う |
入荷時 | 仕入先の納品ミス | ・仕入先に対策をしてもらう |
保管時 | 紛失・盗難 | ・3定管理を徹底する |
出荷時 | 誤出荷 | ・共通の対策を徹底する |
データ処理 | 入力ミス・漏れ | ・数字やアルファベットの書き方を統一する |
「システム導入」では、下記種類から自社の状況に合ったものを選ぶようにしましょう。
システム導入はコストがかかりますが、効率化によるコストカットと、時代のキャッチアップのためにも、前向きに導入を検討してみてください。
【差異削減につながるシステム】
基幹システム | 商品情報を読み取る機器 |
・在庫管理システム ・倉庫管理システム(WMS) | ・ハンディターミナル ・スマートフォン ・RFIDタグ対応ハンディターミナル ・重量センサー、など |
本記事が差異の削減に役立てば幸いです。
#棚卸し #差異
コメント